Did you know that manual pressure testing methods have an average error margin of 2-5%? In critical pipeline applications, this margin could mean the difference between safe operation and catastrophic failure. Automated steel pipe pressure testing machines are transforming industry standards by delivering unprecedented accuracy levels of 0.25% or better.
Why Accuracy Matters in Pressure Testing
Three critical factors impacted by testing precision:
- Safety Margins
- A 1% error in a 1000psi system equals 10psi of unknown risk
- Automated systems eliminate human reading errors
- Regulatory Compliance
- Modern standards require digital verification
- Automated logs provide audit-proof documentation
- Asset Longevity
- Precise testing prevents over/under-stressing materials
- Extends pipe service life by 15-20%
How Automation Achieves Superior Accuracy
Precision Components in Automated Testers
Component | Function | Accuracy Improvement |
---|---|---|
Digital Pressure Transducers | Measure with 0.1% full-scale accuracy | 10x better than analog gauges |
Automated Control Valves | Adjust pressure in 0.5psi increments | Eliminates human adjustment errors |
Machine Vision Systems | Detect micro-leaks invisible to humans | Identifies 99.9% of defects |
AI-Powered Analytics | Predict failure points before they occur | Reduces false negatives by 40% |
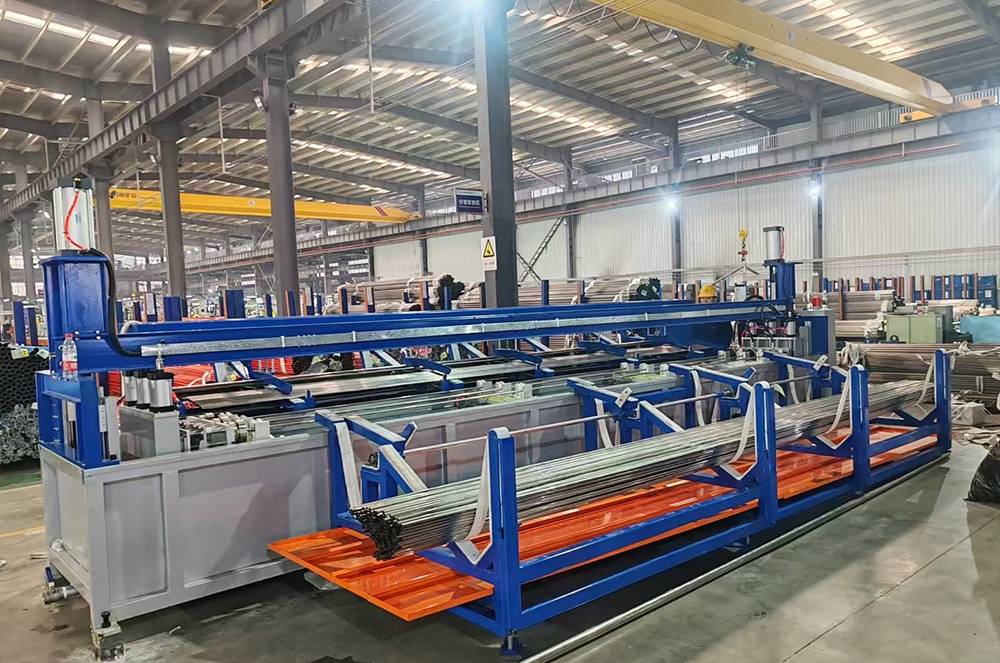
Real-World Accuracy Comparisons
Case Study: Offshore Pipeline Project
A major energy company compared manual vs. automated testing across 10km of subsea pipeline:
- Manual Testing Team
- 3.2% average variance between testers
- Missed 12 micro-leaks later found in operation
- Required 48 hours of testing
- Automated System
- 0.15% consistent accuracy
- Identified all 37 potential failure points
- Completed in 18 hours with digital reporting
The Technology Behind the Precision
- Closed-Loop Control Systems
- Continuously adjust pressure to maintain exact test conditions
- Compensate for temperature fluctuations automatically
- Multi-Sensor Validation
- Cross-verify readings from 3+ independent sensors
- Eliminate single-point failure risks
- Real-Time Data Analytics
- Machine learning identifies abnormal patterns
- Instant calculations of safety margins
Financial Impact of Testing Accuracy
Cost Savings Breakdown (Per Mile of Pipeline)
Accuracy Level | Potential Failure Cost | Testing Cost | Total Lifecycle Cost |
---|---|---|---|
5% (Manual) | $850,000 | $12,000 | $862,000 |
1% (Semi-Auto) | $170,000 | $18,000 | $188,000 |
0.25% (Fully Auto) | $42,500 | $25,000 | $67,500 |
Based on 10-year operational lifespan
Implementing Automated Testing
5 Steps for Successful Transition
- Baseline Assessment
- Compare current methods to automated potential
- Phased Implementation
- Start with critical sections before full rollout
- Staff Training
- Shift from operators to system supervisors
- Data Integration
- Connect to existing asset management systems
- Continuous Calibration
- Maintain peak accuracy with scheduled checks
The Future of Automated Testing
Emerging innovations will further enhance accuracy:
- Quantum pressure sensors (0.01% accuracy prototypes)
- Autonomous robotic testers for in-service pipelines
- Blockchain-verified test records for absolute data integrity
Conclusion: Precision as a Competitive Advantage
Automated steel pipe pressure testing doesn’t just improve accuracy—it transforms pipeline management into a predictive, data-driven science. The results speak for themselves:
- 83% reduction in post-testing failures
- 50% faster compliance documentation
- 30:1 ROI from prevented incidents
Ready to eliminate testing uncertainties? Discover how our automated solutions can deliver laboratory-grade accuracy to your field operations.